
Simonelli Group è partner di una serie di progetti innovativi cofinanziati dal Fondo europeo di sviluppo regionale:
MERCURY (sMart sEcuRe deCentralized indUstRY)
Simonelli Group è partner del progetto di ricerca MERCURY (sMart sEcuRe deCentralized indUstRY) che propone la realizzazione di una piattaforma di automazione industriale per l’Industry 4.0 integrando tecnologie di Edge Computing con tecniche di Cybersecurity e Distributed Ledger Technologies (DLT).
Il progetto mira ad affrontare nuove sfide tecnologiche grazie alla decentralizzazione della computazione, l’esecuzione di logiche sicure basate sull’uso di Smart Contracts, integrando elementi di intelligenza artificiale per la comprensione del dato in tema di tolleranza e/o prevenzione dei guasti e monitoraggio delle misure e di attuazione di tipo cyber-fisico, ottimizzazione dei processi industriali.
Il Progetto HD3FLab (Human Digital Flexible Factory of the Future Laboratory) è nato a seguito dell’iniziativa della Regione Marche che, utilizzando il Fondo Europeo di Sviluppo Regionale, ha deciso di promuovere lo sviluppo di quattro piattaforme tecnologiche di ricerca collaborativa, sviluppo ed innovazione negli ambiti della specializzazione intelligente.
Nella primavera del 2018 una compagine di 23 aziende private ed enti pubblici, con capofila Filippetti SpA e il coordinamento scientifico dell’Università Politecnica delle Marche, ha presentato il progetto HD3FLab, rivolto alle applicazioni caratterizzanti il tessuto industriale ed artigianale marchigiano quali ad esempio il mobile, la calzatura, l’abbigliamento e la meccanica.
L’idea di fondo del progetto, poi sviluppato negli anni 2018-2022, era studiare soluzioni attraverso le quali il sistema di produzione possa garantire la necessaria efficienza nella realizzazione di piccoli lotti e prodotti personalizzati e dove l’uomo e la tecnologia convivano in modo efficace.
In questo contesto, il progetto HD3FLab si è posto, e ha poi raggiunto, i seguenti obiettivi specifici:
· Permettere lo studio di nuovi sistemi/approcci per supportare la produzione flessibile e i metodi per lo human-centered manufacturing
- Aumentare la conoscenza delle aziende partner sulle tecnologie abilitanti del paradigma Industria 4.0 e legate allo sviluppo di sistemi flessibili di produzione e della fabbrica human-centered
- Permettere lo studio di soluzioni innovative per le quali la tecnologia acquisita durante lo sviluppo del progetto venga modificata e personalizzata per rispondere alle esigenze produttive di specifiche tipologie di prodotto o servizio delle aziende partner
- Aumentare la collaborazione tra ricercatori universitari ed aziende, in particolare PMI, attraverso uno spazio comune dove affrontare e risolvere insieme casi specifici
- Diffondere la cultura dell’Industria 4.0 coinvolgendo studenti delle scuole secondarie, degli ITS e delle Università.
Il progetto HD3FLab ha coinvolto 19 imprese private, l’Università Politecnica delle Marche e l’Università di Camerino, Meccano e la Fondazione Cluster Marche e si è sviluppato su 5 diverse linee di intervento.
Meccano ha coordinato il progetto di trasferimento tecnologico, che ha consentito di implementare in 5 diversi contesti applicativi alcune importanti tecnologie di Industria 4.0, quali la realtà virtuale, la tracciabilità, la robotica collaborativa, il data mining.
Fondazione Cluster Marche ha curato la diffusione, disseminazione e valorizzazione dei risultati della ricerca e delle attività di trasferimento tecnologico. Il centro dell’intero progetto HD3FLab è stata la creazione del Laboratorio i-Labs Industry, nato negli spazi messi a disposizione dal Comune di Jesi, con lo scopo di mettere a punto e testare le ricerche sviluppate nel progetto e di permettere alle aziende del progetto di sperimentare le tecnologie di Industria 4.0.
All’interno del progetto è stato avviato un caso studio di manutenzione predittiva applicato alle macchine professionali per caffè espresso Simonelli Group. Use case Nuova Simonelli | i-Labs
Il caso d’uso prevede lo sviluppo di nuovi modelli “smart” di utilizzo e manutenzione di macchine da caffè (Nuova Simonelli). Questo approccio permette una gestione del funzionamento (implementazione di azioni di ripristino e/o correzione delle modalità operative) anche da remoto poiché le macchine sono costantemente sotto controllo.
L’analisi dei parametri rilevati e associati ad uno specifico fault della macchina in fase di uso permette di derivare un algoritmo predittivo basato sull’intelligenza artificiale e sul machine learning in modo che sia possibile intervenire su una macchina prima del fault sostituendo i componenti di cui si prevede la rottura a breve. Queste attività permettono di raggiungere nuovi livelli di integrazione e avanzamento dei processi aprendoli a nuove funzionalità e servizi.
I temi che hanno la principale relazione con questo caso d’uso sono: AI e big data nell’ottica della manutenzione predittiva.
Integrazioni rispetto agli obiettivi del caso d’uso: sono stati selezionati due modelli di macchine da caffè prodotte da Nuova Simonelli con i relativi dati post-vendita. Sono stati considerati inoltre i relativi dataset di collaudo al fine della ricerca di eventuali correlazioni tra le manutenzioni delle macchine da caffè e i guasti in fase di esercizio presso i clienti. I dataset rappresentano gli elementi essenziali per contestualizzare l’ambito della ricerca in merito alle tecniche di Intelligenza Artificiale che possono essere applicate e la corretta scelta delle tecniche di analisi dei dati.
Sviluppo del caso d’uso: i dataset di collaudo e post-vendita delle macchine da caffè sono stati integrati nei processi di analisi dati al fine per l’addestramento dei modelli predittivi. Questi processi si caratterizzano per le fasi di ingegnerizzazione e l’individuazione delle caratteristiche nei dati che meglio descrivono i parametri di funzionamento delle macchine da caffè sia in fase di collaudo che di esercizio. Grazie all’analisi della correlazione rispetto ai guasti verificati nel tempo, è stato possibile addestrare modelli di Machine Learning per poter riconoscere in automatico tali condizioni e anticiparle nel tempo.
Valorizzazione dei risultati: i modelli e le tecniche di analisi dei dati di collaudo e produzione sulle macchine da caffè hanno permesso di definire nuovi approcci alle tecniche di AI nel contesto industriale. Questo permette di migliorare ed efficientare gli interventi di manutenzione nel tempo rispetto ai classici interventi programmati.
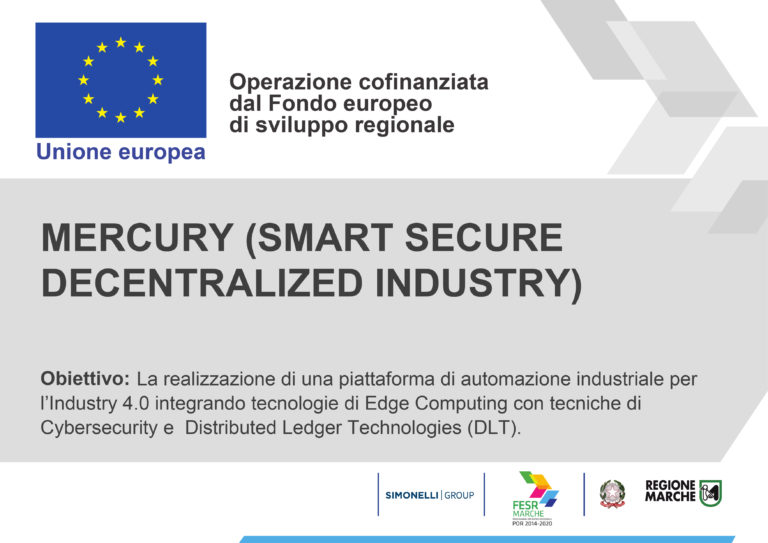
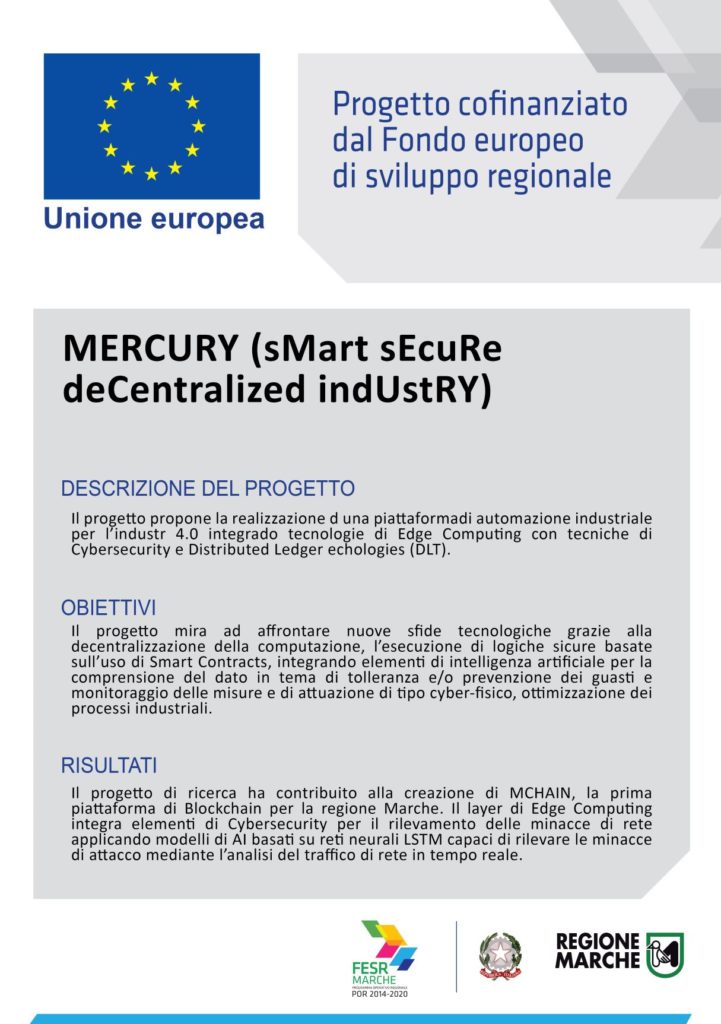
MARLIC – Marche Applied Research Laboratory for Innovative Composites
Simonelli Group è partner del progetto MARLIC – Marche Applied Research Laboratory for Innovative Composites co-finanziato dalla Regione Marche nell’ambito del POR MARCHE FESR 2014-2020. Il Progetto, prevede un gruppo di lavoro di 27 soggetti guidati dall’impresa capofila HP Composites, leader a livello mondiale nella progettazione e produzione di componenti in materiale composito avanzato. Insieme ad HP anche 20 aziende, la Fondazione Cluster Marche e cinque centri di ricerca tra cui l’Università di Camerino, l’Università Politecnica delle Marche, l’Università degli Studi di Urbino, ENEA e CNR.
MARLIC è la piattaforma della Regione Marche nell’ambito della “Manifattura sostenibile: eco-sostenibilità di prodotti e processi per nuovi materiali e de-manufacturing”.
Il progetto ha come obiettivo la realizzazione di un laboratorio regionale di ricerca collaborativa nelle aree colpite dal sisma sui temi dell’eco-sostenibilità di prodotti e processi per i nuovi materiali e sul demanunfacturing. Il laboratorio è il cuore pulsante attorno al quale si sviluppano due progetti di ricerca, un progetto di trasferimento tecnologico e uno di disseminazione dei risultati. Le attività svolte sono indirizzate al sostegno del sistema industriale marchigiano per la modernizzazione e diversificazione di prodotti e processi produttivi, attraverso lo sviluppo di materiali compositi di origine bio e il recupero degli scarti di produzione, di componenti a fine vita e di materie prime/seconde dai cicli di produzione.
Contesto
Qualsiasi azienda che produce beni genera dei sottoprodotti come scarti e sfridi di lavorazione, e genera dei prodotti di fine vita. Gli scarti sono differenti per tipologia di produzione, per natura e per costo di smaltimento. Il composito è il più complesso dei materiali poiché costituito da componenti di natura diversa, spesso difficilmente separabili e recuperabili.
Problema
Ogni anno tali scarti aumentano di volume e il loro costo di smaltimento risulta sempre maggiore, come maggiore è la difficoltà delle aziende e delle discariche di stoccarli, trasformarli e recuperarli. Questa problematica genera la necessità di diminuire le quantità di scarti prodotte, di riutilizzarle come materia prima seconda e di smaltire solo la quota che non riesce a trovare collocazione nel recupero.
Soluzione
Progettazione innovativa mediante applicazione di metodologie e strumenti di DFD – Design for Demanufacturing e DFR – Design for Recycling che utilizzi materie prime facilmente recuperabili, che impieghi materiali riciclati e che individui processi ecocompatibili.
Dopo l’individuazione delle tipologie e delle quantità di scarti/sfridi di prodotto e delle loro caratteristiche, gli scarti diventeranno, dopo adeguato trattamento, risorsa per altre produzioni oppure materia prima seconda per la stessa produzione. Saranno identificate le migliori tecnologie di recupero/trasformazione e valutato il loro impatto ambientale.
Risultati Attesi
Attraverso la definizione di metodologie di progettazione innovativa, di nuove possibilità di impiego del materiale recuperato, della realizzazione di componenti prototipali, tutto il know-how acquisito sarà condiviso da tutti i partner del progetto e dei centri di ricerca. Si avrà una completa caratterizzazione dei componenti pilota realizzati con i materiali di recupero per valutare il loro impiego in campi di applicazione trasversali al mondo produttivo marchigiano.
Investimento totale: 11.434.208,66 €
Finanziamento pubblico: 6.400.197,70 €
Maggiori informazioni: www.marlic.it – simonelligroup.com/economia-circolare-e-la-macchina-da-caffe/
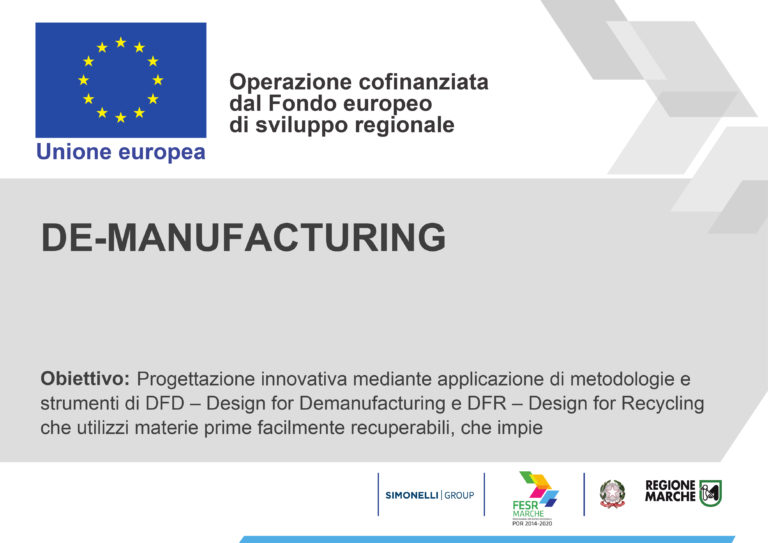
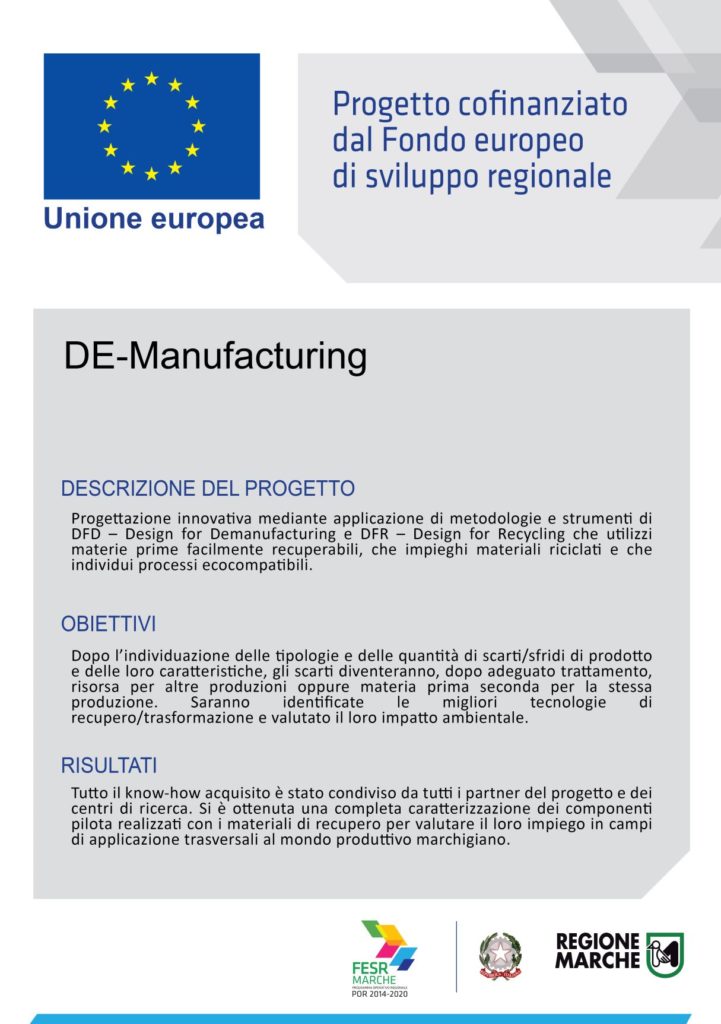
SIMPLE – Smart Manufacturing Machine with Predictive Lifetime Electronic maintenance
Il progetto Smart Manufacturing Machine with Predictive Lifetime Electronic maintenance (SIMPLE) ha come obiettivo lo studio e lo sviluppo di innovativi prodotti in grado di implementare logiche di manutenzione predittiva, connessi a un’inedita piattaforma altamente flessibile (applicabile, con minimi interventi di configurazione, alle diverse tipologie di prodotto oggetto di studio), dai costi contenuti (tali cioè da non incidere in maniera significativa sul costo totale dell’apparato sul quale verrà integrata), pensata in modo tale da non sconvolgere né complicare le funzionalità e l’utilizzo dei prodotti ed esportabile, in generale, anche ad altri contesti industriali in quanto applicabile a qualsiasi apparato distribuito sul territorio.
Il progetto in esame è presentato da 5 grandi imprese, con sede operativa nella regione Marche e ben radicate nel tessuto socioeconomico locale:
- SIGMA, promotrice del progetto in questione e azienda capofila, specializzata nella produzione e gestione di apparecchiature elettroniche quali bancomat, biglietterie automatiche ferroviarie, esazione pedaggi e parcheggi, gestione attese, segnalamento ferroviario, sistemi di sicurezza e sorveglianza.
- Clabo, azienda leader nella produzione di vetrine refrigerate e arredamenti per il food retail.
- Simonelli Group, azienda leader nella progettazione e realizzazione di macchine per caffè espresso.
- Schnell, azienda leader a livello mondiale nella produzione di macchine automatiche per la lavorazione del ferro per cemento armato per il settore delle costruzioni (rebar).
- Pieralisi, leader mondiale nella produzione di impianti e macchine olearie nonché nella produzione di impianti per la separazione centrifuga.
Gli apparati sviluppati grazie al progetto di R&D saranno dotati di apposita sensoristica e, comunicando con la piattaforma, trasferiranno i dati necessari affinché la stessa, dopo averli elaborati, possa prevedere in anticipo gli eventi che potrebbero pregiudicarne il funzionamento.
Il monitoraggio remoto identifica e tiene traccia dello stato operativo corrente e dei parametri di funzionamento di un apparato; la manutenzione predittiva invece analizza i trend, trova le correlazioni ed individua dei modelli che sarebbero molto difficili o addirittura impossibili da individuare altrimenti, focalizzando l’attenzione su eventi futuri e non ancora accaduti: mentre la tele assistenza ed il controllo da remoto rappresentano, per alcune delle proponenti, una realtà oramai consolidata, la manutenzione predittiva è una novità per tutte.
La predictive maintenance rappresenta un’alternativa più vantaggiosa rispetto alle pratiche oggi comunemente seguite per ripristinare la funzionalità e l’efficienza di macchinari ed attrezzature. Allo stato attuale, la manutenzione più seguita è la manutenzione correttiva o a guasto, che consiste nell’intervenire, con riparazioni o sostituzioni, solo a seguito del verificarsi di un malfunzionamento per ripristinare lo status quo ante. Questo tipo di manutenzione presenta dei limiti intrinseci dovuti principalmente al fatto che, molto spesso, comporta costi elevati per mancata produzione derivanti dal fermo macchina, nonché costi dovuti alla riparazione del macchinario stesso. Una politica di manutenzione meno seguita è quella preventiva ciclica: dopo aver individuato i componenti critici di un apparato, si provvede alla loro sostituzione secondo uno scadenzario periodico, indipendentemente dalle loro condizioni reali. Ciò permette di limitare i costi delle perdite di funzionalità a seguito di guasti, di programmare meglio l’utilizzo degli operatori addetti, di organizzare il magazzino ricambi e di ridurre i tempi di fermo impianto ma, d’altro canto, può portare ad effettuare interventi non necessari sacrificando una parte della vita utile del componente ed inoltre, per motivi di tempo e denaro, non riguarda tutti i componenti dell’apparato, lasciando quelli meno a rischio alla manutenzione correttiva. La manutenzione predittiva risulta essere la strategia di manutenzione che offre i maggiori vantaggi, in quanto: permette di minimizzare i costi di manutenzione ed i tempi di inattività della macchina, offre la possibilità di attivare nuovi business perseguibili grazie alla possibilità di pianificare in modo ottimizzato il servizio di assistenza, permette di organizzare al meglio l’intervento in termini di approvvigionamento del componente sostitutivo e di programmare il fermo di produzione necessario per la realizzazione della manutenzione, rendendolo così meno impattante sui ritmi produttivi, permette di sfruttare al massimo la vita utile di ogni componente di un apparato, evitando costi per manutenzione non realmente necessaria. Nonostante ciò, la Predictive Maintenance è ad appannaggio di pochissime aziende, principalmente in ragione del fatto che le soluzioni esistenti sono fortemente personalizzate, coperte da massima riservatezza e basate su grandi capacità di calcolo che richiedono strutture tecnologiche adeguate, ovviamente costose e, dunque, possibili solo per enti, grandi organizzazioni o multinazionali.
Scopo del progetto è quello di sviluppare un sistema altamente innovativo proprio perché economico ed universale, che sia in grado di effettuare delle correlazioni intelligenti per permettere di prevedere in anticipo possibili malfunzionamenti dei prodotti. Il sistema di manutenzione predittiva utilizzerà i dati provenienti dalla periferia, correlando le grandezze misurate e stimando la probabilità che avvenga un guasto tramite tecniche di machine learning e deep learning. A tal proposito verrà sviluppata una piattaforma software volta al monitoraggio da remoto dei parametri macchina più indicativi dello stato di funzionamento degli apparati, i quali verranno individuati grazie alle analisi ed agli studi che saranno effettuati da ogni partner, inerentemente al proprio prodotto, nelle fasi iniziali del progetto. Al fine di rendere il sistema quanto più possibile flessibile nell’ambito del progetto, lo stesso verrà implementato e validato sulle diverse realtà di cui i partner sono i leader indiscussi. La piattaforma software potrà comunicare con gli apparati distribuiti nel territorio tramite uno o più protocolli di comunicazione che emergeranno dalla fase di studio; i prodotti delle aziende facenti parte del partenariato saranno i casi applicativi su cui verrà applicata e validata la piattaforma.
Il progetto verrà avviato con lo studio e la definizione dei parametri e delle grandezze, tipiche di ciascuna macchina prescelta, maggiormente rilevanti ai fini della manutenzione predittiva. Nello specifico verranno svolte le seguenti attività:
- Approfondita analisi della macchina in termini dei suoi principi di funzionamento, delle segnalazioni di eventuali criticità o problematiche specifiche, e delle casistiche delle rotture della stessa; questi dati di campo e l’analisi di eventuali dati storici delle macchine saranno valutate in termini di coerenza rispetto alla manutenzione predittiva.
- Definizione di un modello strategico manutentivo idoneo e, di conseguenza, dell’elenco dei parametri da monitorare e le modalità con le quali intercettare i guasti.
- Studio della architettura hardware con tutto quanto riguarda la scelta dei sensori; fondamentale sarà la definizione delle tipologie, delle caratteristiche e del posizionamento degli stessi al fine di poter rilevare in modo ottimale ed attendibile i parametri precedentemente definiti e reputati utili. Sarà indispensabile quindi definire il sistema di integrazione e di connessione dei sensori applicati per poter raccogliere in modo utile tutte le informazioni acquisite e poterle successivamente processare in attesa di essere trasmesse alla piattaforma centrale.
- Studio del traduttore, cioè di un sistema in grado di adattare i dati provenienti da ciascuna macchina, secondo protocolli accettati dalla piattaforma centrale, realizzando in questo modo una gestione omogenea per tutti i casi di studio definiti.
Al termine della fase di ricerca saranno poste milestones intermedie, in quanto le attività si completeranno con una validazione di concetto delle ipotesi di riconoscimento guasto implementato sui singoli simulacri realizzati. Solo a questo punto avrà inizio la fase di sviluppo all’interno della quale si andranno a realizzare i primi prototipi completi e ad integrare gli stessi con la piattaforma di manutenzione predittiva. Nel dettaglio, le attività eseguite saranno:
- Realizzazione prototipale dei sistemi di monitoraggio per ciascuna delle macchine scelte da ogni azienda partner: in tale fase avverrà quindi il posizionamento dei sensori prescelti nonché la revisione completa delle macchine dal punto di vista meccanico ed elettronico così come definito nell’ambito della precedente fase di studio.
- Realizzazione delle schede elettroniche per integrazione e connessioni dei sensori di rilevamento al fine di poter predisporre la successiva fase finale del processo dei dati acquisiti su ciascuna macchina monitorata.
- Controllo, verifica e validazione dei sistemi prototipali realizzati.
A queste attività si aggiungerà quella legata alla realizzazione prototipale del traduttore, fase questa fondamentale per rendere fruibili da parte della piattaforma tutti i dati acquisiti dalle macchine cosi strumentate e monitorate.
La fase finale di validazione della piattaforma prototipale per manutenzione predittiva così realizzata, sarà messa in atto dalla azienda capofila e permetterà di chiudere le attività di iniziale ricerca industriale e la successiva fase di sviluppo sperimentale costituenti il presente progetto.
Da quanto sopra esposto si evince chiaramente che il punto di forza dell’innovazione contemplata nella realizzazione del programma che le cinque aziende intraprenderanno è lo sviluppo di soluzioni flessibili e standardizzabili applicabili a qualsiasi apparato distribuito sul territorio. Si tratta di un progetto molto ambizioso che si inserisce in maniera decisamente innovativa nel panorama nazionale e internazionale di riferimento, in quanto consentirà di sviluppare una nuova best technology italiana inerente sia la piattaforma che i nuovi prodotti ad essa connessi rispetto al miglior stato dell’arte nazionale ed internazionale.
Parte Simple, 5 aziende in rete per i sensori che prevengono i guasti – Il Sole 24 ORE
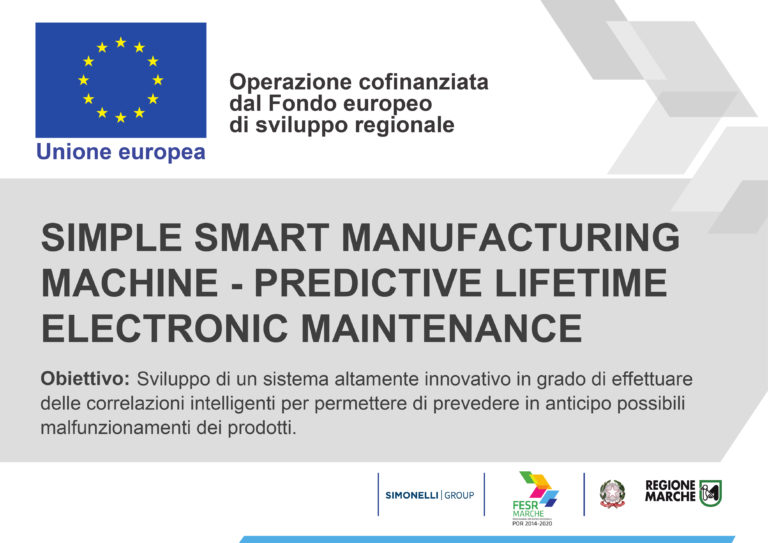
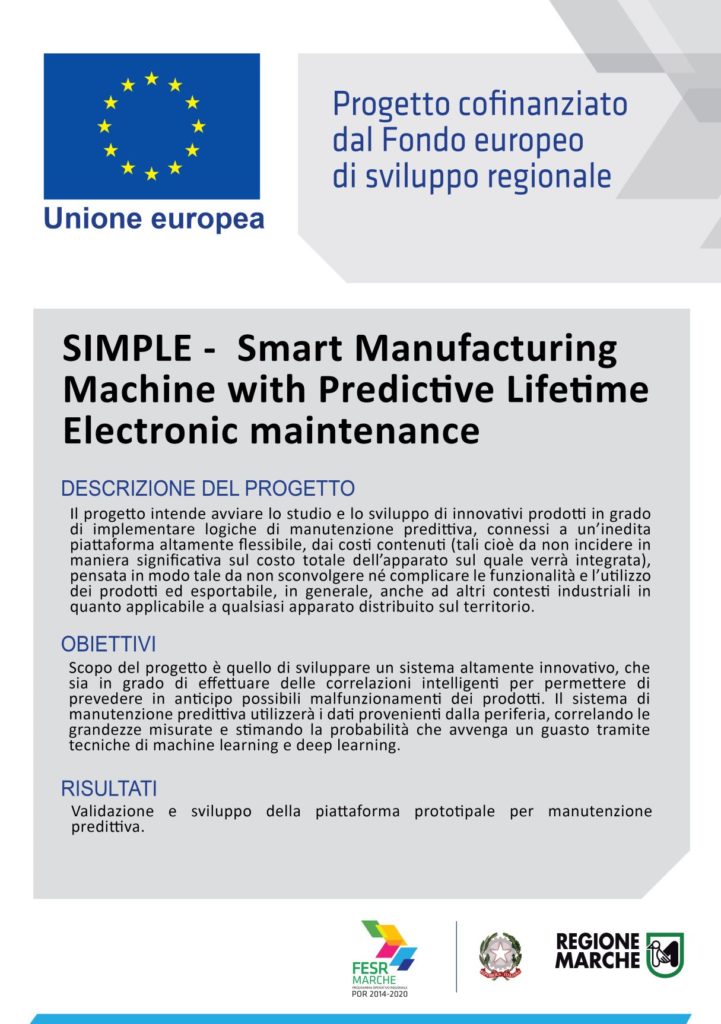